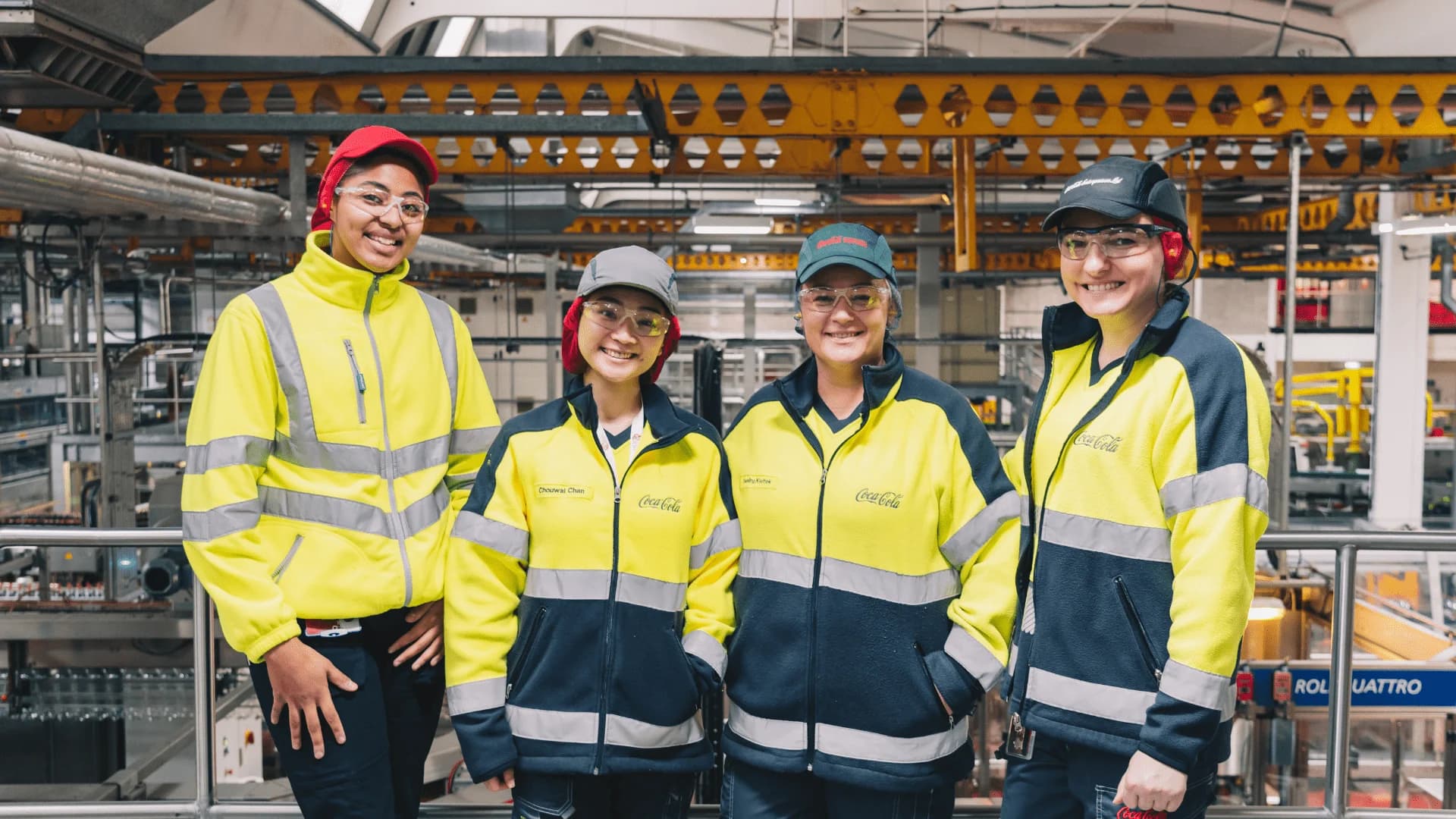
Supply Chain Opportunities
United Kingdom, Multiple Locations - Apprentices
Vacancy details
- Category:
- Apprentices
- Salary:
- 0
Supply Chain Opportunities
What is Supply Chain?
Our supply chain function is the heart of the production, manufacturing and distribution of our products, from the purchase of ingredients and packaging to manufacturing and distribution to our customers. Our machines can produce over 100,000 bottles an hour. We also have teams who look after the Quality of our product and ensure its safe for everyone to enjoy! Coca-Cola and many of our other soft drinks start life as a base syrup. Very few people know the secret recipe of a Coke and to protect it, the syrup arrives at our GB factories in two parts, which need to be mixed in the right proportions. Once mixed, we dilute the syrup with water and add sugar or sweetener to it. If it’s sparkling, we add carbon dioxide to give the fizz, and then fill and package bottles or cans on automated production lines ready to be delivered to our customers. We are focused on ensuring we have the manufacturing and distribution capacity to meet our customer requirements, and also driving operations performance through improving efficiency and effectiveness, and sharing and executing best practice.
What skills do you need to work in Supply Chain?
• Strong communication skills
• Good eye for detail
• Ability to work under pressure and problem solve
• Able to work as part of a team or alone, with little supervision
• Adaptable and flexible to change
What opportunities do you have?
There are a number of ways to join our Supply Chain team:
Operator Technician
Reporting into a Shift Manager working as part of our production team to safely operate and maintain machinery and production lines. Carrying out routine machine maintenance and basic repairs and recording quality checks. Using route cause analysis to diagnose and escalate any faults and supporting Engineers to improve line reliability. The operator technicians need to uphold Food Safety and Health and Safety Regulations and requires elements of manual handling.
Warehouse
Our Distribution Centres are 24/7 operations and consist of Automated Storage and Retrieval System (ASRS) warehouses holding anything between 15,000 to 30,000 pallets of stock. Our largest site, Wakefield, also houses a block-stacked conventional warehouse holding an additional 20,000 pallets. Inbound vehicles also arrive from our other factory sites with palletised goods which must be put away promptly and safely into the ASRS and accurately recorded. Our Warehouse teams have to promptly and safely stack away goods; record and locate stock using SAP and Locator stock management systems and assemble orders ready for dispatch to our customers.
Material Planning
You will be a part of the GB Planning & Commercialisation Department which includes: Commercialisation, Demand Planning, Production Planning, Materials Planning, Allocation and Deployment. You will be based in the heart of our operations, at the Corporate Head Office in Uxbridge, London. The materials that the team manage include all components required to enable finished goods production of Coca Cola soft drinks e.g. glass bottles, resin, pallets, labels, film, cans and sugar. The team are responsible for ensuring the continuous supply of all materials (primary, secondary and tertiary) into six manufacturing sites across the UK.
Production Planning
You will be a part of the GB Planning & Commercialisation Department which includes: Commercialisation, Demand Planning, Production Planning, Materials Planning, Allocation and Deployment. You will be based in the heart of our operations, at the Corporate Head Office in Uxbridge, London. The Production Planning team are responsible for the creation and execution of the production plans of our six manufacturing sites. The team are responsible for ensuring that we maintain optimal stock levels to deliver the supply plan to our retailers across the UK.
Demand Planning
You will be a part of the GB Planning & Commercialisation Department which includes: Commercialisation, Demand Planning, Production Planning, Materials Planning, Allocation and Deployment. You will be based in the heart of our operations, at the Corporate Head Office in Uxbridge, London. The Demand Planning Team are responsible for delivering the annual Business Plan volumes to enable the growth of CCEP. As a Demand Planner you will be responsible for the forcast of a specific group of SKUs and customers across the UK.
Customer Logistics & Transport Roles
Our Nottingham Customer Logistics Centre are responsible for order taking, delivery and building strong collaborative supply chain relationships with our customers including grocery retailers, wholesalers, retails outlets and brewers in Great Britain. There are 2 pillars within the Logistics Centre which are Customer Service and Transport who all work in partnership to drive the right service and supply chain efficiencies for our business and our customers. Our Logistics team in Nottingham are a high performing, fast paced, engaged and customer centric team that prides itself on being our customers preferred supplier. Guided by our shared values we thrive in an environment where collaboration and openness are valued. We are passionate about developing people within our teams and as such are famous for nurturing talent and exporting them to other areas of the business.
QESH
You will be part of the Quality, Environment, Safety & Health (QESH) team. This team performs a governance role, ensuring that we are in line with legal and Coca-Cola requirements. Your role will also support the wider QESH team in delivery of business wide activities, such as auditing, training, coaching and communication.
What qualifications do I need?
• Eligibility to work in the UK
• Some roles will require lifting and handling of stock, full manual handling training will be provided
Click apply now to view all current opportunities